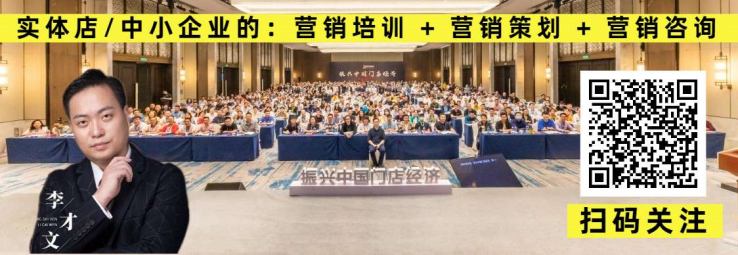
在紧固件行业中,螺栓的扭矩系数测试是衡量产品品质及预防螺栓失效的关键指标。那么,在进行紧固件扭矩系数测试时,我们需要注意哪些事项呢?
首先需知,螺丝扭矩系数出现问题大多源于两个方面。其一为产品本身的设计问题,包括潜在的结构缺陷和制造缺陷。其次则是人工装配过程中可能出现的问题。若装配人员在操作过程中施加的扭力过大或过小,都可能为紧固件的失效埋下隐患。随着温度的变化,金属材料的热胀冷缩也会影响产品的夹持力,从而可能导致紧固件的失效。
本文旨在详细分析因装配工艺不当导致的紧固件扭矩系数失效情况。
装配不当引起的紧固件扭矩系数问题主要有两大根源。一是人为因素导致的装配错误,二是机器设备故障引发的装配失误。材料的稳定性和操作方法的合理性也是影响扭矩系数的关键因素。
鉴于上述原因,过去在设定锁紧螺丝的扭力时,通常依赖经验值。为何设定这样的值往往没有明确的解释。虽然理论上可以通过计算公式来确定扭力,但这一过程涉及多种材料的摩擦系数和螺纹的参数,相当复杂。特别是对于小型电子产品用的螺丝(如M3及以下),供应商往往无法提供螺丝的屈服强度等关键参数,这使得理论计算变得更为困难。
为了更准确地确定扭力参数,我们可以使用螺栓扭矩系数检测仪进行性试验。通过此试验,我们可以绘制出扭力变化曲线图,从而找出固定扭力和滑牙扭力,并制定一个合适的扭矩取值范围。
在进行性试验前,需遵循以下步骤:
对于钣金件螺丝通孔,需精确测量板材厚度t和孔的拉伸高度h,因为不同的板材厚度对应的滑牙扭力值是有所区别的。
要确保工件孔径尺寸符合设计规范。使用不同规格的塞规或投影仪测量孔径尺寸,以确保其处于设计规格内。理想的样品应能覆盖从下限到上限的所有尺寸,这样才能更全面地反映各种极限情况下的扭力变化趋势。
在验证过程中,所使用的零件仅能使用一次,不可重复利用。因为一些难以察觉的损坏或残留异物可能会影响曲线数据的采集,从而导致错误的结论。
试验时,需确保零件有稳定的工装固定,电批保持垂直。如有条件,可以利用扭力臂保证垂直度,以避免因工件随意晃动而影响曲线图的正常输出。
将控制器、电批和电脑连接起来,设置电批参数。然后进行不同螺丝和不同位置的性试验,收集扭力曲线图数据。
螺丝扭力标准的设定方法
通过性试验和所收集的扭力曲线数据(至少120组数据),找出其中最大的固定点力矩和最小的滑牙扭力。然后,根据这些数据通过简易公式计算出合适的力矩。
滑牙扭矩是指螺丝固定过程中测得的最大扭矩,当发生滑牙时,螺丝将在连接件中自由转动,这时扭矩会减小,角度会增大。
固定扭矩则是指螺丝帽接触到工件表面时,扭力曲线开始产生突变的那一点所对应的扭矩。
下图展示了固定塑胶自攻螺丝的性示例曲线图。根据此图,我们可以找出两个关键的扭力值,进而计算扭力的设定范围。
虽然力矩的理论计算能提供一定的指导,但考虑到实际制造过程中的众多变量和参数选择,实际拧紧过程与理论计算可能存在一定差距。利用智能电批和相应的数据采集软件进行实际装配的性试验,能更直观地反映螺丝从空转到被的整个过程。这样的计算方法更接近制造现场的实际操作,也更易于理解和接受。
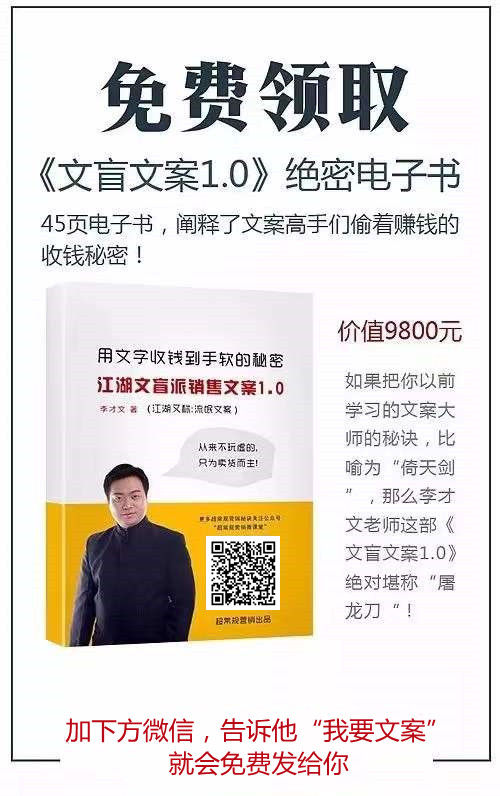