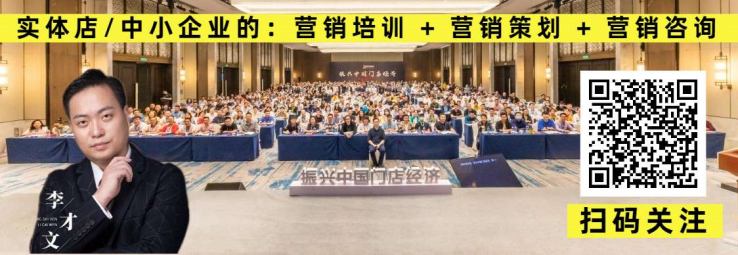
两大管理体系的巅峰对话
一、DMAIC与价值流图的较量
核心武器:DMAIC(定义、测量、分析、改进、控制)以其严谨的流程著称。
杀手锏:利用统计学精确找出质量变异之根源。
经典案例:某芯片厂通过DMAIC,将晶圆缺陷率从8%降低至0.5%,年节省成本高达2.3亿。
核心武器:价值流图、5S与快速换模,以消除浪费为目标。
杀手锏:让价值流动更为顺畅,如滑翔般高效。
经典案例:某汽车厂通过实施价值流图,消除了搬运浪费,物流效率提升40%。
六西格玛如同手持“显微镜”细察质量,而精益生产则如“望远镜”远观流程。当两者相融合,便构成了全方位的“全息投影”。
二、四个行业的融合实战
问题一:变速箱壳体加工线产能不足,关键尺寸合格率低。
融合改造方案:
① 精益开路:利用价值流图发现时间浪费点,优化流程。
② 六西格玛攻坚:通过假设检验锁定问题根源,设计防错工装。
成果展示:产能提升、合格率提高、库存减少。
问题二:患者等待时间长,急救设备取用差错率高。
融合改造措施:
① 精益优化流程:绘制患者流动图,消除重复环节。
② 六西格玛控质量:建立监控机制,双人核查防呆机制。
成果展示:患者满意度提高,差错率归零。
问题三:大促期间错发率高,订单处理速度慢。
融合改造策略:
① 六西格玛基础建设:锁定错发原因,设计标签系统。
② 精益提效:实施拣货法改进,开发协同算法。
成果展示:错发率降低,处理能力增强,人力成本下降。
三、三步走向完美融合
1. 专家引领:黑带专家负责质量难题的,运用数据分析方法。
2. 教练执行:精益教练负责现场改善,推动线平衡及拉动式生产。
3. 融合秘诀:定期的数据+现场联合诊断会,确保双方有效沟通。
某家电企业实践表明,实时数据监控及现场管理的重要性,异常情况能及时触发改善流程。
四、避开融合路上的障碍
错误做法与方案:
1. 质量部与生产部的矛盾:通过成本换算,明确效率损失。
2. 办公室与现场的脱节:推行“三现”数据采集,确保现场实时反馈。
3. 标准与改善的平衡:建立双轨文件系统,既守标准又持续改善。
五、未来工厂的新形态
随着技术的发展,未来工厂将融入数字孪生、AI预警及动态平衡等技术,实现精益与六西格玛的完美结合。当数据与现场相得益彰时,制造业将进入新的进化阶段。
六、公司介绍与经营理念
深圳华昊联合企业管理顾问有限公司(华昊企管),自2012年以来,以精益管理咨询为核心,致力于帮助企业提质、降本、增效、创新。我们秉持用心服务、诚信共赢的经营理念,不断深入研究行业应用,升级咨询服务体系,确保项目落地见效。凭借独特的驻厂手把手辅导模式及多年经验,我们在解决企业复杂问题和动员全员参与改善方面深受客户赞誉。
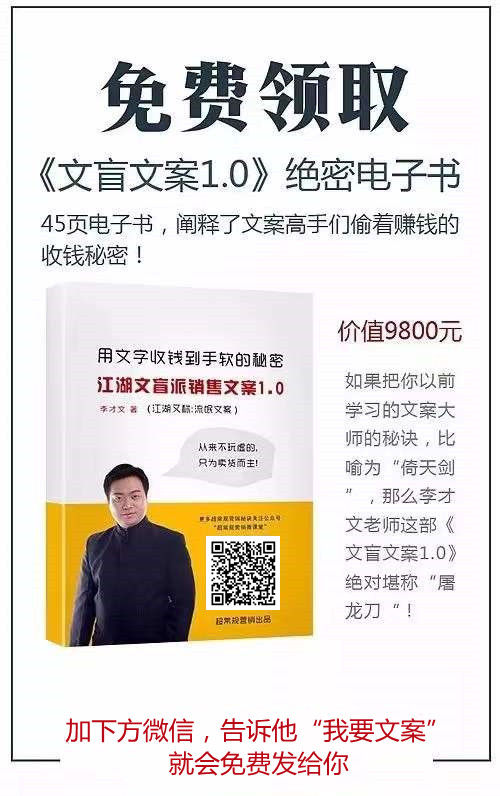