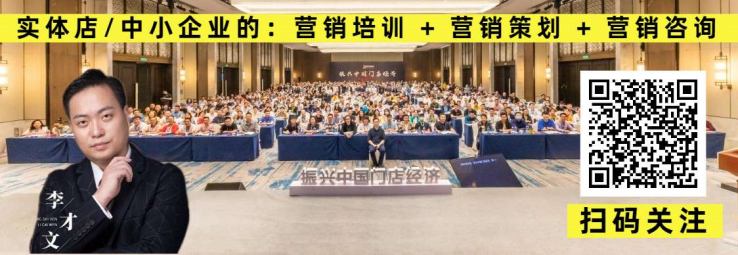
无损检测,简称NDT(Non Destructive Testing),亦称无损探伤。此技术能在不损伤被检对象的形态和内部结构的前提下,对被检对象的内部和外部的物理、力学性能以及缺陷和其他技术参数进行测定和评价。
根据缺陷的所在位置,无损检测方法主要分为表面检测方法和内部检测方法。
表面检测方法详述:
涡流检测(ECT)
磁粉检测(MT)
渗透检测(PT)
内部检测方法详述:
射线检测:包括射线检测(RT)、计算机X射线照相(CR)、数字射线成像(DR)
超声检测:包括超声检测(UT)、超声波衍射时差法(TOFD)
声发射检测(AE)
今日重点介绍工业CT检测与其他内部检测方法的特性。(于文末简述各检测方法的应用情况,如表1所示。)
超声检测技术中,超声检测(UT)是最为常见的常规检测方法。它通过超声波与试件的相互作用,对试件进行宏观缺陷检测、几何特性测量以及和力学性能变化的检测和表征。
图1:展示了超声检测(UT)的原理。
超声检测的优点在于设备轻便、操作安全,并易于实现自动化检验。其具有较大的穿透能力,例如在钢中可探测深度达一米以上。对于平面型缺陷如裂纹、夹层等,探伤灵敏度较高,并能测定缺陷的深度和相对大小。
它不适合检测几何形状复杂的工件,且被检查表面需保持一定的光洁度。对于某些粗晶粒的铸件和焊缝,因易产生杂乱反射波而较难应用。超声检测的结果不直观,需要经验丰富的检验人员进行操作和判断。
接着是超声波衍射时差法(TOFD)。这是一种依靠从被检工件内部缺陷的“端点”处得到的衍射波在扫描线上的时差来检测缺陷尺寸的方法。
图2:阐释了超声波衍射时差法(TOFD)的工作原理。
TOFD的优点包括检测灵敏度高、操作便捷和实时成像。它对缺陷的定性较为困难,不适用于复杂几何形状的工件,且对缺陷走向不敏感,近表面存在盲区。
至于射线检测技术,RT、CR、DR通常对被检工件的某个角度进行照相,可能存在缺陷信息被内部结构或其他缺陷覆盖的情况。而工业CT检测则通过使被检工件进行360°旋转照相,从而获取更全面的缺陷信息,如缺陷尺寸、位置、方向和类型。
图3至图5:分别展示了RT、CR、DR及工业CT的工作原理。
各种射线检测技术各有优劣,例如RT成本较低但图像质量高;CR为数字化图像易于存储和后处理;DR在图像质量上有较大提升;而工业CT虽成本高、需固定场地,但具有出色的三维成像及数据分析功能。
声发射检测技术(AE)则是当材料或结构件产生形变时,以弹性波形式释放出应变能的现象。利用接收声发射信号研究其内部情况。
图6:阐释了声发射检测技术(AE)的工作原理。
声发射检测技术适用于实时动态监测,仅检测正在形变/扩展的缺陷以确定其危险程度,而不涉及缺陷的具体尺寸、位置和方向。此技术成本低、操作简单并可实时观测结果,受材料性能和的影响较小。
总结以上所述,无损检测方法的应用特点已列于表1(随后附上表格)。
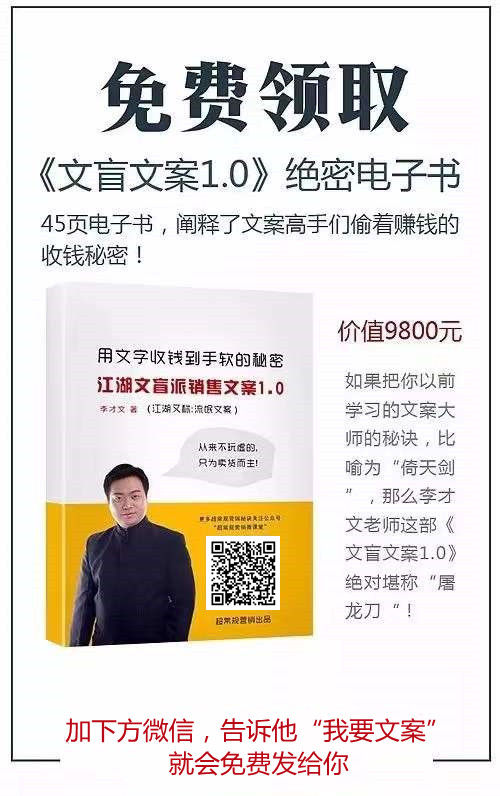